Worlds First Laser 3D-Printed Knee Implant Unveiled by Naton Biotechnology and Research Partners
25 views
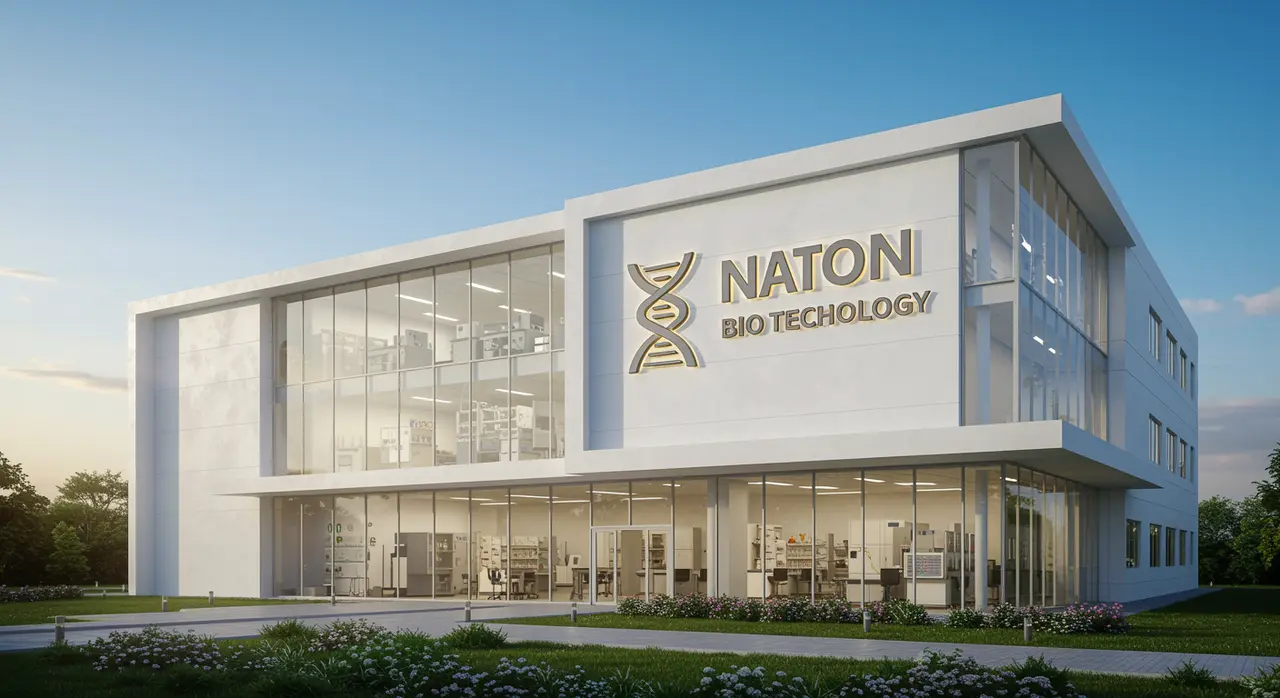
In a groundbreaking stride for orthopedic medicine, researchers at Naton Biotechnology have unveiled the world's first laser 3D-printed total knee implant, a marvel of engineering now officially approved by China's National Medical Products Administration as an innovative medical device. This achievement not only marks a pivotal moment for medical technology but also signals a transformative leap forward in the manufacturing of safer, stronger, and more reliable implants, a prospect that promises to reshape the landscape of orthopedic care.
Forging Strength and Precision: The Science Behind the Breakthrough
At the core of this revolutionary advancement lies a meticulous reimagining of the cobalt-chromium-molybdenum (CoCrMo) alloy, a material long favored for its durability and biocompatibility in medical implants. The team at Naton Biotechnology, collaborating with experts from South China University of Technology and Beijing Tsinghua Changgung Hospital, employed a laser powder bed fusion (LPBF) process to construct the implant—a technique that uses high-intensity lasers to fuse powdered metal into precise, intricate designs layer by layer. However, the inherent challenges of 3D printing, such as anisotropy and uneven material strength, presented formidable hurdles.
To address these issues, the researchers devised a two-step heat treatment protocol that proved to be the linchpin of their success. The process begins with a solution treatment at 1150°C, which reorganizes the alloy’s microstructure to enhance uniformity. This is followed by annealing at 450°C, a step that fine-tunes the material’s mechanical properties, achieving an equilibrium between strength and flexibility. The results were nothing short of remarkable: mechanical tests revealed the treated CoCrMo alloy exhibited near-identical tensile strength and elongation in all directions, effectively eliminating the inconsistencies that have long plagued 3D-printed implants.
The implications of this achievement are profound. By ensuring uniformity and robustness in every dimension, the new implants promise greater reliability under the daily stresses of movement and weight-bearing. For patients undergoing total knee replacement—a procedure that demands precision and durability—the enhanced properties of these implants could translate into improved outcomes and extended longevity, reducing the need for revision surgeries and enhancing quality of life.
A Future of Endless Possibilities
While the current breakthrough is undoubtedly a milestone, the researchers are already looking ahead to the next frontier. Future studies aim to refine the implants further by enhancing wear resistance and biocompatibility, two critical factors in ensuring the long-term success of orthopedic devices. Techniques such as shot peening and ultrasonic peening are being explored to fortify the surface of the implants, making them more resilient against the microscopic abrasions and stresses that accumulate over time. Additionally, advancements in biocompatibility could pave the way for implants that integrate more seamlessly with human tissue, minimizing the risk of rejection and promoting faster recovery.
The publication of these findings in Materials Futures underscores their significance within the scientific community. By shedding light on the intricate interplay between material science and medical engineering, the study not only sets a new benchmark for 3D-printed implants but also opens the door to broader applications. From hip replacements to spinal implants, the principles established here could catalyze innovation across a range of orthopedic solutions, bringing us closer to a future where personalized, high-performance medical devices are the norm.
The Human Element: Bridging Science and Patient Care
Beyond the technical triumphs, this development carries profound implications for patient care. Total knee replacement surgeries are among the most common orthopedic procedures worldwide, yet they are fraught with challenges, including implant failure and post-operative complications. The advent of stronger, more consistent 3D-printed implants could alleviate many of these concerns, offering patients a safer and more reliable option tailored to their unique anatomical needs.
Moreover, the use of 3D printing introduces a level of customization that traditional manufacturing methods cannot match. By leveraging advanced imaging technologies, surgeons could design implants that conform precisely to a patient’s joint structure, optimizing fit and function. This personalized approach could not only enhance surgical outcomes but also reduce recovery times, allowing patients to regain mobility and independence more quickly.
Reflection: A New Era of Medical Innovation
The creation of the first laser 3D-printed total knee implant represents more than just a technological achievement; it is a testament to the power of interdisciplinary collaboration and the relentless pursuit of progress. By bridging the worlds of material science, engineering, and medicine, the researchers have charted a path toward a future where medical devices are not only stronger and safer but also more attuned to the needs of individual patients.
As we stand on the cusp of this new era, it is worth considering the broader implications of such advancements. The integration of 3D printing into medical manufacturing has the potential to democratize access to high-quality implants, reducing costs and expanding availability to underserved populations. Furthermore, the adaptability of this technology could spur innovation in other areas of healthcare, from prosthetics to surgical tools, transforming the way we approach treatment and recovery.
In the end, the story of Naton Biotechnology’s breakthrough is one of possibility—a reminder that with ingenuity and perseverance, the boundaries of what is achievable in medicine are constantly expanding. As researchers continue to refine and build upon this foundation, the promise of better, more personalized care for millions of patients around the world feels not just within reach but inevitable.